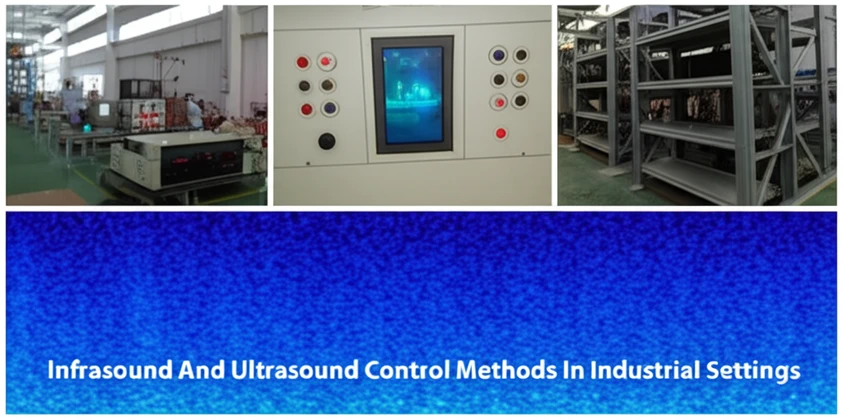
In today’s increasingly complex industrial environments, the presence of inaudible sound waves like infrasound and ultrasound poses significant challenges to worker safety, equipment integrity, and regulatory compliance. While often overlooked, effective infrasound and ultrasound control methods in industrial settings are critical for maintaining a productive and healthy workplace.
This article delves into the intricacies of infrasound and ultrasound control, exploring their sources, potential impacts, and the most effective mitigation strategies. From traditional noise control techniques to cutting-edge innovations, we’ll examine how industries can address these unseen challenges and create safer, more efficient work environments.
What Are Infrasound and Ultrasound?
Both infrasound and ultrasound reside outside the range of human hearing, but their effects on industrial settings can be substantial.
Understanding their characteristics is the first step toward effective control.
Infrasound
Infrasound comprises sound waves with frequencies below 20 Hz. These low-frequency vibrations are often generated by large-scale equipment and processes. Examples include:
- Heavy Machinery: Reciprocating compressors (e.g., Ingersoll Rand Centac centrifugal compressors), large diesel engines (e.g., Wärtsilä RT-flex96C), and industrial turbines (e.g., Siemens SGT-800 gas turbine) often produce significant infrasound during operation.
- Ventilation Systems: Large-scale HVAC systems, particularly those employing low-speed fans, can generate infrasound that propagates through ductwork and building structures.
- Natural Phenomena: Wind turbines (specifically, designs with larger rotor diameters) and geological processes like earthquakes are natural sources of infrasound.
Effects of Infrasound
- Health Impacts: Prolonged exposure to high-intensity infrasound can lead to a range of symptoms, including headaches, fatigue, sleep disturbances, dizziness, and anxiety.
Research suggests that infrasound may affect the vestibular system and inner ear, contributing to these symptoms. (Leventhall, 2007)
- Structural Concerns: Resonance, a phenomenon where infrasound amplifies vibrations in structures with similar natural frequencies, can lead to fatigue and eventual failure in sensitive machinery or infrastructure.
Ultrasound
Ultrasound encompasses sound waves with frequencies above 20,000 Hz. In industrial settings, ultrasound is commonly encountered in various applications:
- Ultrasonic Cleaning Devices: Devices using ultrasonic cavitation for cleaning (e.g., those operating at 20-40 kHz) are prevalent in many industries.
- Welding Equipment: Ultrasonic welding processes often employ frequencies in the 20-40 kHz range to generate localized heat and fuse materials.
- Non-Destructive Testing (NDT): Ultrasonic testing equipment (e.g., using frequencies from 0.5 MHz to 20 MHz) is used to detect flaws in materials.
Effects of Ultrasound
- Health Risks: Occupational exposure to high-intensity airborne ultrasound can cause auditory effects such as tinnitus and hearing shifts, as well as non-auditory effects like nausea and headaches.
(Lawton, 2001)
- Equipment Malfunctions: High-frequency sound waves can interfere with the operation of sensitive electronic equipment, potentially leading to malfunctions or data corruption.
Importance of Infrasound and Ultrasound Control in Industrial Settings
Managing both infrasound and ultrasound is crucial for several reasons:
Worker Safety
Uncontrolled exposure to infrasound and ultrasound can pose serious risks to worker health and well-being. Mitigating these risks is a moral and legal imperative.
- Hearing Loss and Other Auditory Effects (Ultrasound): Prolonged exposure to high-intensity ultrasound can lead to permanent hearing damage.
- Physiological and Psychological Effects (Infrasound): Infrasound exposure can cause various symptoms, including fatigue, headaches, and psychological distress, impacting worker productivity and overall well-being.
Equipment Efficiency
Excessive noise and vibration, including infrasound and ultrasound, can contribute to premature wear and tear on machinery, increasing maintenance costs and reducing operational efficiency.
Effective control measures can extend equipment lifespan and minimize downtime.
Regulatory Compliance
Numerous regulatory bodies, including OSHA (Occupational Safety and Health Administration) in the United States and various ISO (International Organization for Standardization) standards, mandate noise control measures to ensure worker safety. For example, OSHA’s 29 CFR 1910.95 pertains to occupational noise exposure, while ISO 1996-2 provides guidelines for assessing community noise. Effective management of infrasound and ultrasound helps organizations comply with these standards and avoid penalties.
Methods for Controlling Infrasound in Industry
Source Isolation
Isolating machinery at the source is a primary strategy for minimizing infrasound transmission.
This involves physically separating the noise-generating equipment from the surrounding environment.
- Acoustic Enclosures: Specialized enclosures designed using materials with high sound transmission loss (STL) at low frequencies, such as heavy-mass concrete or multi-layered composite panels, effectively contain infrasound. Proper sealing and ventilation design are critical for effectiveness.
- Vibration Isolators: Spring mounts, rubber pads, or air-based isolators placed between machinery and the supporting structure decouple vibrations and prevent transmission to the surrounding environment.
Selection of appropriate isolators depends on the machinery’s weight and operating frequency.
Structural Dampening
Applying dampening materials to structures can reduce the amplitude of infrasound vibrations. This involves converting vibrational energy into heat, dissipating the sound energy.
- Viscoelastic Materials: Specialized damping compounds, like those based on polymers or bitumen, are effective at absorbing low-frequency vibrations. These materials are applied as coatings or incorporated into structural elements.
- Mass-Loaded Vinyl (MLV): Dense vinyl sheets added to walls, floors, or ceilings add mass and reduce the transmission of low-frequency sound.
Active Noise Control (ANC)
ANC systems employ sophisticated technology to counteract infrasound by generating anti-noise.
This involves sensing the incoming infrasound wave and creating a counter-wave that cancels it out.
- Microphones: Specialized microphones detect the infrasound wave’s amplitude and phase.
- Signal Processors: Digital signal processors (DSPs) analyze the incoming wave and generate a counter-wave with an inverted phase.
- Loudspeakers: Loudspeakers emit the counter-wave to neutralize the original infrasound.
- Challenges and Limitations: ANC is most effective in controlled environments and for specific frequency ranges. It can be complex to implement and calibrate, particularly for broadband infrasound sources.
Methods for Controlling Ultrasound in Industry
Shielding and Barriers
Creating barriers around ultrasonic equipment confines high-frequency sound waves.
This involves using materials that effectively reflect or absorb ultrasound.
- Acoustic Panels: High-density foam panels or those with micro-perforated surfaces absorb ultrasound effectively. Their performance is dependent on thickness and material properties.
- Metallic Shields: Thin sheets of metal, such as aluminum or stainless steel, can reflect ultrasound waves, preventing their propagation into the workspace. The effectiveness depends on the material’s density and the ultrasound frequency.
- Curtains and Enclosures: Flexible acoustic curtains or enclosures made of heavy vinyl or specialized fabrics can provide localized shielding around ultrasonic equipment.
Personal Protective Equipment (PPE)
Providing workers with appropriate PPE is essential in high-exposure areas. This includes hearing protection specifically designed to attenuate ultrasonic frequencies.
- Specialized Earmuffs: Earmuffs designed for high-frequency noise attenuation provide better protection against ultrasound compared to standard earmuffs.
- Ear Plugs: Certain earplug designs offer increased attenuation at higher frequencies.
It’s crucial to select earplugs with appropriate noise reduction ratings (NRR) for the specific ultrasound levels.
Calibration and Maintenance
Regular calibration and maintenance of ultrasonic devices are critical for ensuring safe operation and minimizing unintended sound emissions. This includes verifying power output, frequency stability, and component integrity. Preventive maintenance schedules should be followed meticulously, and any damaged or malfunctioning components should be replaced promptly.
Applications of Infrasound and Ultrasound Control
Manufacturing
- Reducing Infrasound from Heavy Presses: Implementing vibration isolation systems, such as air springs beneath large presses, minimizes infrasound transmission to the factory floor, improving worker comfort and preventing structural fatigue.
- Ultrasound Control in Ultrasonic Welding: Enclosing ultrasonic welding stations within sound-absorbing enclosures and providing workers with appropriate hearing protection minimizes exposure to potentially harmful ultrasound levels.
Medical Industry
- Safety in Medical Imaging: Limiting exposure to ultrasound during diagnostic imaging (e.g., by using lower power settings and optimizing scanning protocols) minimizes potential risks to patients and medical personnel.
- Hygiene Standards for Ultrasonic Cleaning: Ensuring ultrasonic cleaning equipment used for sterilizing medical instruments is properly enclosed and maintained prevents both ultrasound exposure and potential contamination.
Renewable Energy
- Wind Turbine Infrasound Mitigation: Advanced turbine blade designs and optimized siting strategies help minimize infrasound generation and propagation from wind farms, addressing community concerns and regulatory requirements.
- Power Plant Noise Control: Implementing acoustic enclosures and silencers around high-frequency systems in power plants reduces ultrasound emissions and improves the working environment for plant personnel.
Innovations in Sound Control Technology
Smart Sensors
Smart sensors and IoT (Internet of Things) devices are transforming noise monitoring and control by providing real-time data and enabling automated responses.
- Real-time Sound Level Monitoring: Wireless sensor networks can monitor sound levels at multiple locations within a facility, providing continuous data on infrasound and ultrasound exposure.
- Automated Control Systems: When sound levels exceed predefined thresholds, smart systems can automatically trigger mitigation measures, such as activating ventilation adjustments or powering down specific equipment.
AI-Powered Systems
Artificial intelligence and machine learning are enabling more sophisticated and proactive noise control strategies.
- Predictive Maintenance: AI algorithms analyze sensor data, equipment performance logs, and environmental factors to predict potential noise issues before they arise, enabling timely intervention.
- Adaptive Noise Cancellation: Advanced ANC systems using AI can adapt to changing noise profiles and optimize counter-wave generation in real time, improving cancellation effectiveness in dynamic industrial environments.
Advanced Materials
Material science advancements are leading to the development of lighter, more efficient, and environmentally friendly noise control solutions.
- Metamaterials: Artificially engineered materials with unique acoustic properties can effectively absorb or deflect sound waves at specific frequencies, offering highly targeted noise control solutions.
- Bio-based and Recycled Materials: Sustainable acoustic materials made from renewable resources, such as plant fibers or recycled industrial waste, minimize environmental impact while providing effective sound absorption.
FAQ
What is the difference between infrasound and ultrasound?
Infrasound refers to sound waves with frequencies below the human hearing range (20 Hz), while ultrasound refers to frequencies above the human hearing range (20,000 Hz). Both are inaudible but have distinct characteristics and effects.
How does infrasound affect workers?
Exposure to high-intensity infrasound can cause various health effects, including headaches, fatigue, dizziness, nausea, and psychological discomfort, potentially impacting worker productivity and well-being.
Are there specific regulations for infrasound and ultrasound?
While specific regulations for infrasound and ultrasound are still evolving, general noise regulations like OSHA’s 29 CFR 1910.95 in the US and ISO 1996-2 for community noise assessment provide frameworks for managing noise exposure in the workplace and surrounding environments.
Specific industry standards may also apply.
What are the most effective infrasound and ultrasound control methods in industrial settings?
A combination of source control (isolation, enclosures), path control (barriers, shielding), administrative controls (limiting exposure time, worker training), and PPE offers the most comprehensive approach. The specific methods chosen depend on the source’s characteristics, the environment, and the regulatory requirements.
What are the cost considerations for implementing infrasound and ultrasound control measures?
Costs vary widely depending on the chosen methods. Simple measures like PPE are relatively inexpensive, while complex solutions like ANC systems or specialized acoustic enclosures can be more costly.
A cost-benefit analysis considering potential health impacts, productivity gains, and regulatory compliance is crucial.
Conclusion
Effective management of infrasound and ultrasound control methods in industrial settings is paramount for ensuring worker safety, optimizing equipment performance, and complying with regulatory requirements. By understanding the nature of these inaudible sound waves and implementing appropriate control strategies, from traditional noise reduction techniques to innovative technologies, industries can create healthier, more productive, and compliant work environments.
Continuous monitoring, advancements in material science, and the integration of AI-powered solutions promise even more effective and targeted noise control strategies in the future. By embracing these advancements, industries can proactively mitigate the risks associated with infrasound and ultrasound, fostering a safer and more efficient work environment for all.